Trim
The Valtek Sulamericana GLS and GLH Series Control Valve Trim are developed to eliminate issues normally associated with valves with threaded seats or cage-guided plug designs. Since the seat is not threaded, but is fixed onto the body by meansof the bonnet and the seat retainer, its removal is quite simple, even when the valve operates in corrosive conditions.
In contrast to trim with a guide in the seat retainer, which is easily susceptible to wear and jamming, the GLS and GLH series trim are guided by a double upper guide system that avoids contact between the seat retainer and the plug. Since there is no direct contact with the plug, the retainer may be manufactured in materials such as stainless steel, instead of costly hardened materials. The flow characteristic is determined by the plug shape, instead of by openings located in the retainer.
For services with very high differential pressures, a pressure-balanced trim design is used to reduce the thrust needed to stroke the plug through the reduction of off-balance trim areas.
Control valves with pressure-balanced trim should be used with clean fluids only, considering also that flow direction for the safety fail-closed position is under the plug, and for the fail-open position is over the plug.
Optionally, the GLS and GLH series control valves may be supplied with the special trim to attenuate the noise level and for applications in which cavitation conditions exist.
Trim Sizes
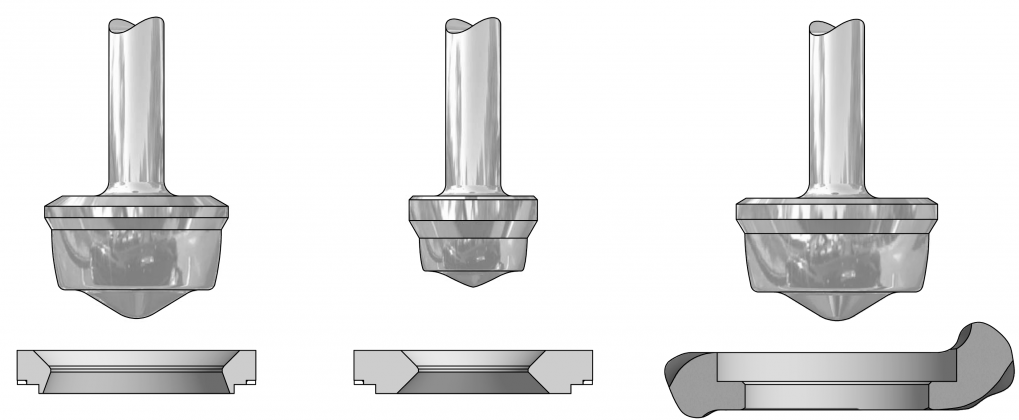
Two sizes of trim are normally available: the standard size, with full-area trim; and the second size with reduced area trim. Reduced area trims are available in a wide variety of dimensions, which are necesssary when the required CV , due to the process conditions, is relatively small for a specific body size intended to be used. In additoin to these options, an integral trim may be supplied, which uses a special seat machined onto the valve body and an oversized plug to provide an even large CV that the CV provided by the standard full-area trim.
As the GLS and GLH control valve trim are completely interchangeable by body size and pressure class, the change of trim size and valve nominal CV is a very simple operation.
Unbalanced Trim
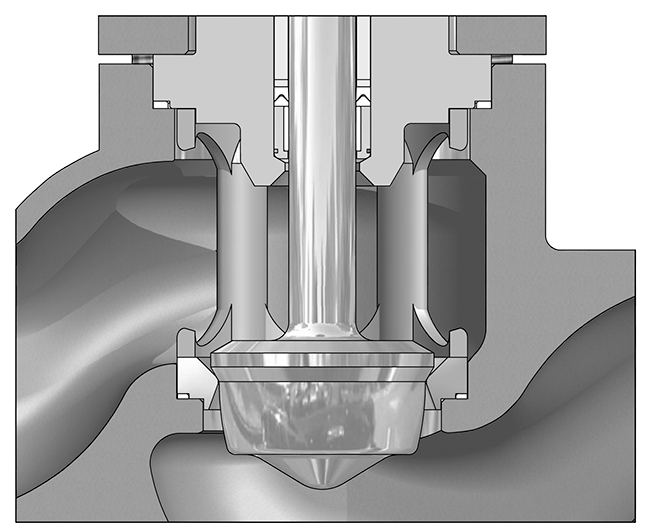
Balanced Trim
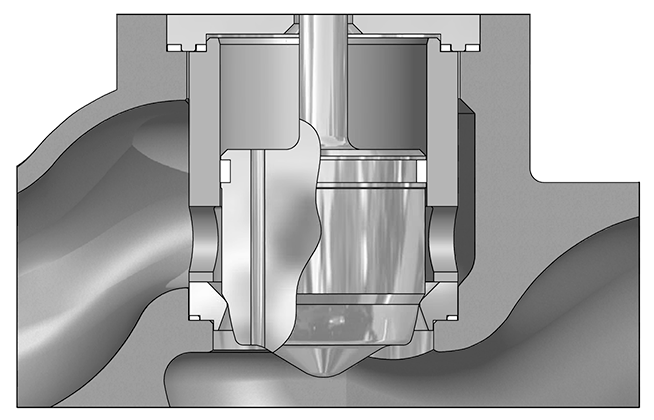
Specification Guide for Pressure-Balanced Plug Seals
Material of Plug Seal1 | Temperature Limits | Shutoff (Metal Seat) | Shutoff (Soft Seat) |
---|---|---|---|
PTFE Seals | −18 to 176°C / 0 to 350°F | up to 10% of Class IV | up to 1% of Class IV |
Reinforced PTFE Seals | −18 to 204°C / 0 to 400°F | up to 10% of Class IV | up to 1% of Class IV |
Buna-N O-Ring | −40 to 93°C / −40 to 200°F | Class IV or V | Class VI |
Viton-A O-Ring | −23 to 204°C / −10 to 400°F | Class IV or V | Class VI |
VMG Metal Seals (2″ to 4″) | 149 to 871°C / 300 to 1600°F | Class III | N/A |
VMG Metal Seals (6″ and larger) | 149 to 871°C / 300 to 1600°F | Class IV | N/A |
1Whenever metal seals such as VMGs are used, the bore surface of the pressure-balanced sleeve must be hardened.
2The temperatuer liits above are for information purposes only.
Contact Valtek Sulamericana to confirm the maximum allowable temperature regarding the operating pressure or when higher leakage classes are required.
Materials
The standard manufacturing material for the GLS and GLH series control valve plug, seat and seat retainer is 316 Stainless Steel, except in cases where special alloys are required or specified. Special alloys such as Duplex, Alloy # 20, Monel., Hastelloy C, Hastelloy B, and other materials, may be supplied on request.
Characteristics of Trim Materials
Trim Materials | Hardness (Rc) | Max Recommended Temperature | Impact Strength | Corrosion Resistance | Erosion Resistance | Abrasion Resistance |
---|---|---|---|---|---|---|
316 SS | 8 | 316°C / 600°F | Excellent | Excellent | Fair | Fair |
Alloy # 6 | 44 | 815°C / 1500°F | Excellent | Excellent | Good | Good |
416 SS | 40 | 425°C / 800°F | Good | Fair | Good | Good |
17-4 PH (H900) | 44 | 426°C / 800°F | Good | Good | Good | Good |
440C SS | 55 – 60 | 426°C / 800°F | Fair | Fair | Excellent | Excellent |
Monel K-500 | 32 | 316°C / 600°F | Good | Good | Fair | Good |
Tungsten | 72 | 650°C / 1200°F | Fair | Good on Bases, Poor on Acids | Excellent | Excellent |
Colmonoy # 5 | 45 – 50 | 650°C / 1200°F | Good | Fair | Good | Good |
Seats
Metal Seats
The GLS and GLH Series control valves by Valtek Sulamericana as standard configuration with an unbalanced trim and metal seat, complies with ANSI B16.104 / FCI 70.2 Class IV, which specifies a maximum allowable leakage of 0.01% of nominal valve capacity.
The exceptional sealing capacity of the GLS and GLH series control valves are easily achieved due to its self-centering seat design. High seat leakage classes are available as an option. Further information can be found in our seat leakage page.
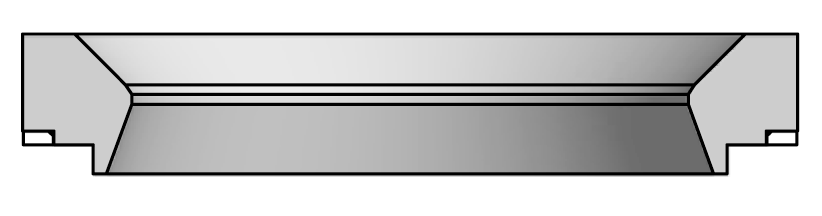
Soft Seats
Soft seats are used in applications requiring extreme tightness, complying with ANSI B16.104 / FCI 70.2 Class IV. The GLS and GLH series control valves soft seats are composed of a polymer assembled between two metal pieces, and it is interchangeable with a metal seat. The soft seat inserts are usually manufactured in PTFE, and therefore the maximum operating temperature shoudl be lower than 150°C @ 20Bar(g). Also available in Fiber Glass and PEEK and other materials depending on the application.
For temperatures below –65°C, soft seats may be used in high-pressure applications.

Hard Facing
As a general rule, hardened trims, such as Alloy # 6 facing, shall be used for all conditions of critical flow or in services where the operating temperature exceed 316°C.
Plug Hard Facing Variation
Seat Surface
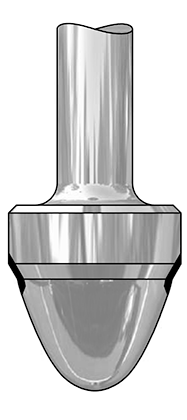
Full Contour
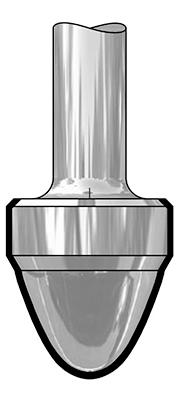
Lower Guide Area
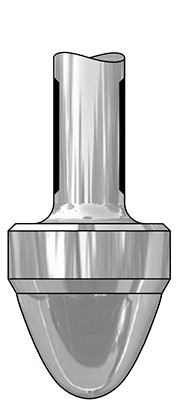
Full Contour & Lower Guide Area
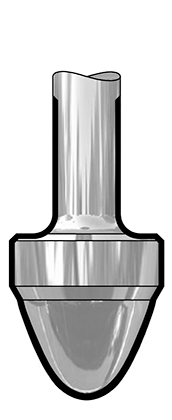
Seat Hard Facing Variations
Hard Facing Seat Area
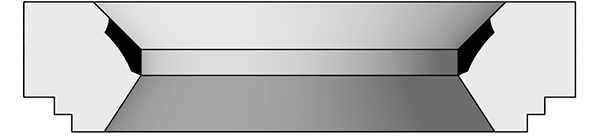
Hard Facing Full Bore
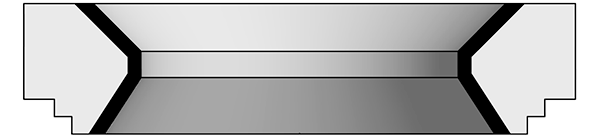
Differential Pressure Values Requiring Hardened Trim
Fluid | 0.5″ to 1.5″ | 2″ & 3″ | 4″ & 6″ | 8″ to 12″ |
---|---|---|---|---|
Water (Throttling) | 175 psi / 12.1 Bar | 150 psi / 10.3 Bar | 100 psi / 6.9 Bar | 50 psi / 3.4 Bar |
Water (On Off) | 250 psi / 17.2 Bar | 200 psi / 13.8 Bar | 125 psi / 8.6 Bar | 100 psi / 6.9 Bar |
Steam Saturated (Throttling) | 100 psi / 6.9 Bar | 25 psi / 1.7 Bar | All Applications | All Applications |
Steam Saturated (On Off) | 200 psi / 13.8 Bar | 50 psi / 3.4 Bar | 25 psi / 1.7 Bar | All Applications |
Steam Super Heated (Throttling) | 300 psi / 20.7 Bar | 200 psi / 13.8 Bar | 100 psi / 6.9 Bar | 50 psi / 3.4 Bar |
Steam Super Heated (On Off) | 600 psi / 41.4 Bar | 300 psi / 20.7 Bar | 150 psi / 10.3 Bar | 100 psi / 6.9 Bar |
Process Fluid General (Throttling) | 175 psi / 12.1 Bar | 150 psi / 10.3 Bar | 75 psi / 5.2 Bar | 50 psi / 3.4 Bar |
Process Fluids (On Off) | 250 psi / 17.2 Bar | 200 psi / 13.8 Bar | 125 psi / 8.6 Bar | 100 psi / 6.9 Bar |
Clean Gases (Throttling) | 600 psi / 41.4 Bar | 350 psi / 24.1 Bar | 200 psi / 13.8 Bar | 125 psi / 8.6 Bar |
Clean Gases (On Off) | 900 psi / 62.1 Bar | 600 psi / 41.4 Bar | 300 psi / 20.7 Bar | 175 psi / 12.1 Bar |